Revolutionizing Efficiency in the Automated Wire Labeler Zone
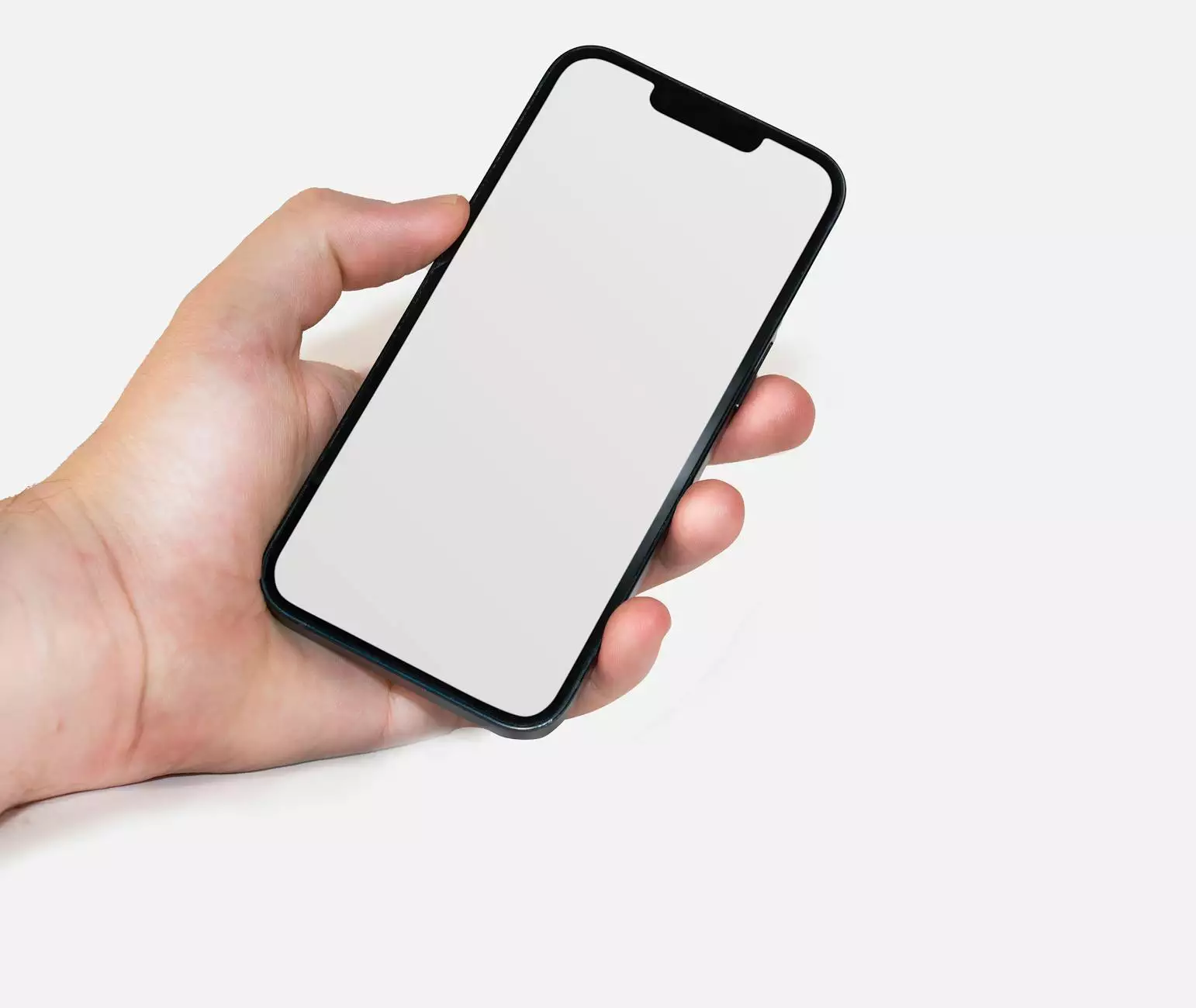
The automated wire labeler zone is rapidly transforming the landscape of packaging. With the continuous evolution of technology, businesses are increasingly turning to automated solutions to enhance efficiency, reduce labor costs, and improve labeling accuracy. In this comprehensive guide, we delve into the burgeoning field of automated wire labeling, its crucial role in the packaging equipment manufacturing sector, and how ShineBen is setting the benchmark in innovation.
The Importance of Automated Wire Labelers
In today's fast-paced industrial environment, the significance of automated wire labelers cannot be overstated. These machines streamline the labeling process, offering numerous advantages:
- Increased Efficiency: Automation drastically reduces the time required for labeling, allowing companies to scale operations and meet rising demands swiftly.
- Enhanced Accuracy: Automated systems minimize human error, ensuring that each label is applied consistently and correctly.
- Cost Reductions: By automating labeling processes, businesses can decrease labor costs and reduce waste, leading to significant savings.
- Flexibility: Modern automated wire labelers can adapt to various wire sizes and label formats, accommodating diverse production needs.
Understanding Automated Wire Labelers
Automated wire labelers are specialized machines designed to affix labels to wires and cables efficiently. These devices vary in complexity and design, ranging from simple label dispensers to advanced systems capable of printing and applying labels in one seamless operation.
At the heart of every automated wire labeler is a labeling head, which can be equipped with various technologies such as thermal transfer, direct thermal, or inkjet printing. The choice of technology influences the quality, durability, and cost of the labels produced:
- Thermal Transfer Printing: This method uses heat to transfer ink from a ribbon onto the label material, resulting in durable and high-quality labels.
- Direct Thermal Printing: This printing method uses heat-sensitive label materials, eliminating the need for ink ribbons, making it cost-effective for short runs.
- Inkjet Printing: Famous for producing high-resolution labels, inkjet printers are ideal for applications requiring intricate designs and high clarity.
Key Components of an Automated Wire Labeler
Understanding the components of an automated wire labeler is essential for selecting the right machine for your needs. Here are some critical elements to consider:
- Labeling Head: As mentioned, this component performs the actual printing and application of labels.
- Label Dispensing Mechanism: This system ensures that labels are fed smoothly from the roll to the labeling head.
- Control Panel: Modern labelers come equipped with user-friendly interfaces, allowing operators to customize settings easily.
- Sensor Systems: These sensors detect the position of wires and synchronize the labeling process for perfect alignment.
- Conveyor Systems: Many automated systems integrate with conveyor belts to streamline the workflow and enhance productivity.
The Advantages of Using Automated Wire Labelers
Investing in automated wire labelers presents several advantages for businesses in the packaging equipment manufacturing domain:
1. Improved Productivity
Automated wire labelers significantly boost productivity by performing tasks faster than human operators. This efficiency allows companies to manage higher volumes of output without compromising quality.
2. Quality Assurance
Quality control is paramount in packaging. Automated labeling ensures that every label is applied consistently, adhering to stringent industry standards, which is vital for product identification and compliance.
3. Labor Optimization
By automating the labeling process, businesses can reallocate labor to more productive tasks, enhancing overall operational efficiency while minimizing labor costs.
4. Faster Time-to-Market
With the ability to label products swiftly and accurately, businesses can reduce their time-to-market, staying competitive in an ever-evolving marketplace.
Sustainability in the Automated Wire Labeler Zone
As the global focus shifts toward sustainable practices, industries are seeking eco-friendly solutions. Automated wire labelers can play a significant role in this regard:
- Reduced Material Waste: Precision labeling minimizes errors and wastage of label materials, contributing to sustainability initiatives.
- Energy Efficiency: Many modern automated systems are designed for energy efficiency, reducing operational costs and environmental impact.
- Use of Recyclable Materials: With advancements in label materials, companies can choose options that are recyclable or biodegradable, aligning with green practices.
Choosing the Right Automated Wire Labeler
Selecting the correct automated wire labeler involves careful consideration of various factors:
1. Production Requirements
Evaluate your production scale. Higher output demands may require robust, high-capacity machines capable of rapid labeling without downtime.
2. Labeling Specifications
Determine the types of labels you need — their size, material, and design will impact the choice of labeler. Ensure the machine can accommodate all your needs.
3. Integration Capabilities
Consider how well the labeling system integrates with your existing production line. Seamless integration is crucial for optimizing workflow.
4. Cost Considerations
Investing in new technology is a significant decision; hence, understanding the total cost of ownership, including maintenance and consumables, is vital.
ShineBen's Leadership in the Automated Wire Labeler Zone
ShineBen stands at the forefront of innovation in the automated wire labeler zone. With years of experience in the packaging equipment manufacturing sector, ShineBen is renowned for its commitment to quality, performance, and customer satisfaction.
Innovative Solutions
ShineBen continually invests in research and development, ensuring that our automated wire labelers are equipped with the latest technology. Features such as:
- Intelligent Control Systems: Optimize production workflows through advanced sensor technology and AI algorithms.
- User-Friendly Interfaces: Simplify operations, making it easy for staff to operate and maintain labeling equipment.
- Customizability: Provide tailored solutions to meet specific client needs, enhancing flexibility and efficiency.
Exceptional Support and Service
When you choose ShineBen, you gain more than just a product; you gain a partner dedicated to ensuring your success. Our comprehensive support includes:
- Consultation Services: Assess your needs and recommend the best solution for your applications.
- Training Programs: Equip your team with the knowledge and skills to operate our machines effectively.
- After-Sales Support: Our commitment to customers continues after the sale, with reliable maintenance and service options.
Conclusion
The future of the automated wire labeler zone is bright and full of promise. As industries evolve and seek more efficient, cost-effective labeling solutions, automated wire labelers will continue to play a vital role. With ShineBen leading the way in innovation and customer service, businesses can confidently invest in technology that drives performance and meets the demands of the modern marketplace.
In conclusion, embracing automation within the wire labeling process not only enhances productivity but also supports sustainability efforts that are increasingly important in today’s economy. Explore how ShineBen can elevate your packaging solutions and be a part of this exciting revolution.