The Excellence of Die Casting: A Deep Dive into Die Casting Mold Companies
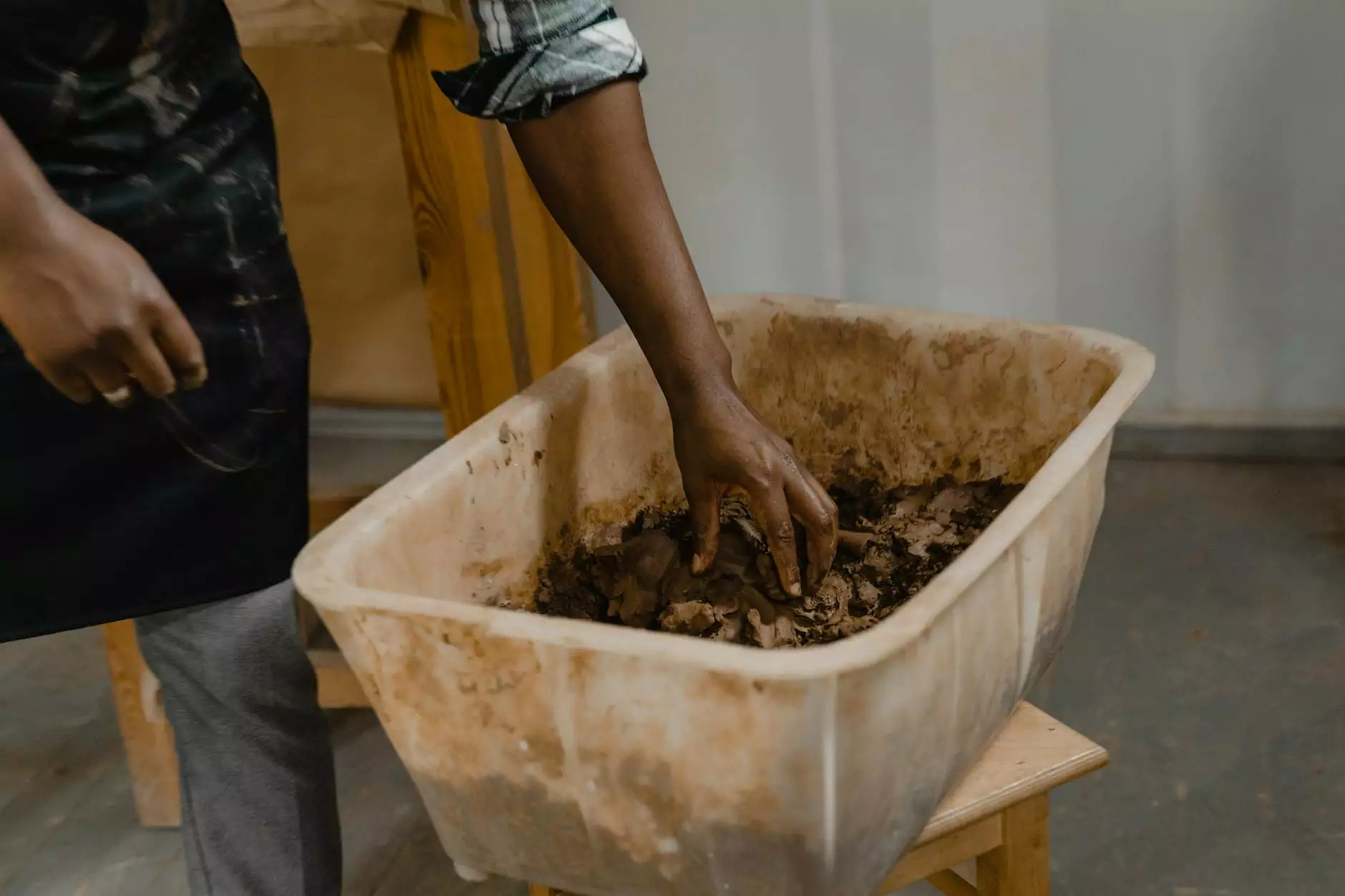
In the ever-evolving world of manufacturing, die casting mold companies play a vital role. These companies specialize in creating precise molds that allow for the efficient and effective production of complex metal parts. Understanding the intricacies of their work not only highlights the significance of these companies but also reveals how they contribute to various industries. At the forefront of this dynamic field is DeepMould, a leader in metal fabrication and die casting solutions.
What is Die Casting?
Die casting is a process where molten metal is injected into a mold under high pressure to form a specific shape. This method is known for its ability to produce complex geometries, high dimensional accuracy, and excellent surface finishes, making it ideal for various applications across numerous industries.
Understanding the Die Casting Process
The Stages of Die Casting
The die casting process can be broken down into several essential stages:
- Preparation of the Mold: The mold must be designed and manufactured to exact specifications for optimal performance.
- Melting the Metal: Metals such as aluminum, zinc, and magnesium are melted in a furnace to attain the desired temperature.
- Injection: The molten metal is injected into the mold at high speed, filling every corner and detail.
- Cooling and Solidification: The metal cools and solidifies rapidly, forming a rigid part that holds its shape.
- Removal: Once the metal has cooled, the mold is opened, and the finished part is removed.
- Trimming: Any excess material, known as flash, is trimmed off to ensure high-quality finishes.
Benefits of Using a Die Casting Mold Company
Choosing a professional die casting mold company like DeepMould has several significant advantages:
- High Precision: The advanced technology involved in die casting allows for exceptionally precise manufacturing, essential for parts that require a high level of accuracy.
- Complex Shapes: Die casting can produce intricate designs that would be difficult or impossible to achieve with other manufacturing methods.
- Cost-Effective: Although initial tooling costs can be higher, the ability to produce large quantities quickly makes die casting highly cost-effective in the long run.
- Excellent Surface Finish: The die casting process provides a smooth finish, reducing the need for extensive surface treatment after production.
- Material Versatility: A wide range of non-ferrous metals can be used in die casting, broadening the scope for various applications.
Applications of Die Casting in Various Industries
Die casting is not confined to a single industry; it serves a plethora of sectors including:
Aerospace
Die casting is used in aerospace for parts like brackets, housings, and other components that demand reliability and lightweight materials. The aerospace industry benefits from the strength and durability of die casted components, which are crucial for flight safety.
Automotive
The automotive sector extensively utilizes die cast parts for engine blocks, transmission housings, and various structural components. The lightweight nature of die cast aluminum significantly enhances vehicle efficiency and performance.
Consumer Electronics
In consumer electronics, die casting molds create enclosures and structural supports for devices where aesthetics and functionality are paramount. The machining flexibility offered by die casting supports innovative designs in the rapidly changing electronics market.
Industrial Equipment
Heavy machinery and industrial equipment often require robust and finely engineered components, which die casting provides. This process ensures that parts can withstand significant wear and tear while maintaining operational efficiency.
Why DeepMould Stands Out as a Die Casting Mold Company
At DeepMould, excellence is not just a goal; it is a guarantee. The company stands out due to its commitment to quality and advanced manufacturing practices. Here are several reasons why DeepMould is a top choice for die casting needs:
- State-of-the-Art Facilities: Equipped with the latest technology, DeepMould adopts innovative techniques to enhance the die casting process.
- Expert Team: The personnel at DeepMould are seasoned professionals dedicated to ensuring every project meets the highest standards.
- Custom Solutions: Understanding that each client has unique needs, DeepMould offers tailor-made solutions to fit various requirements.
- Quality Assurance: Every die casting project undergoes rigorous testing and quality checks to maintain industry certifications and standards.
- Timely Deliveries: DeepMould recognizes the importance of time in manufacturing and places a strong emphasis on meeting deadlines without compromising quality.
The Future of Die Casting Industry
The future of the die casting industry looks promising, with technology playing a central role in its evolution. Automation, advanced alloys, and environmentally conscious practices are set to shape the landscape. As industries push for lighter and stronger materials, die casting will remain at the forefront, paving the way for innovations that meet both market demand and sustainability goals.
Conclusion
In summary, the world of die casting mold companies is intricate and vital to modern manufacturing. With its numerous applications across different sectors, it is clear that die casting offers exceptional benefits that can significantly enhance productivity and product quality. When it comes to high-quality die casting solutions, DeepMould exemplifies what it means to lead the industry with innovative practices, precise engineering, and a focus on client satisfaction. As the demand for efficient and effective metal fabrication continues to grow, partnering with a reliable die casting mold company becomes imperative for businesses looking to stay competitive.