The Power of Plastic Molding Injection in Modern Manufacturing
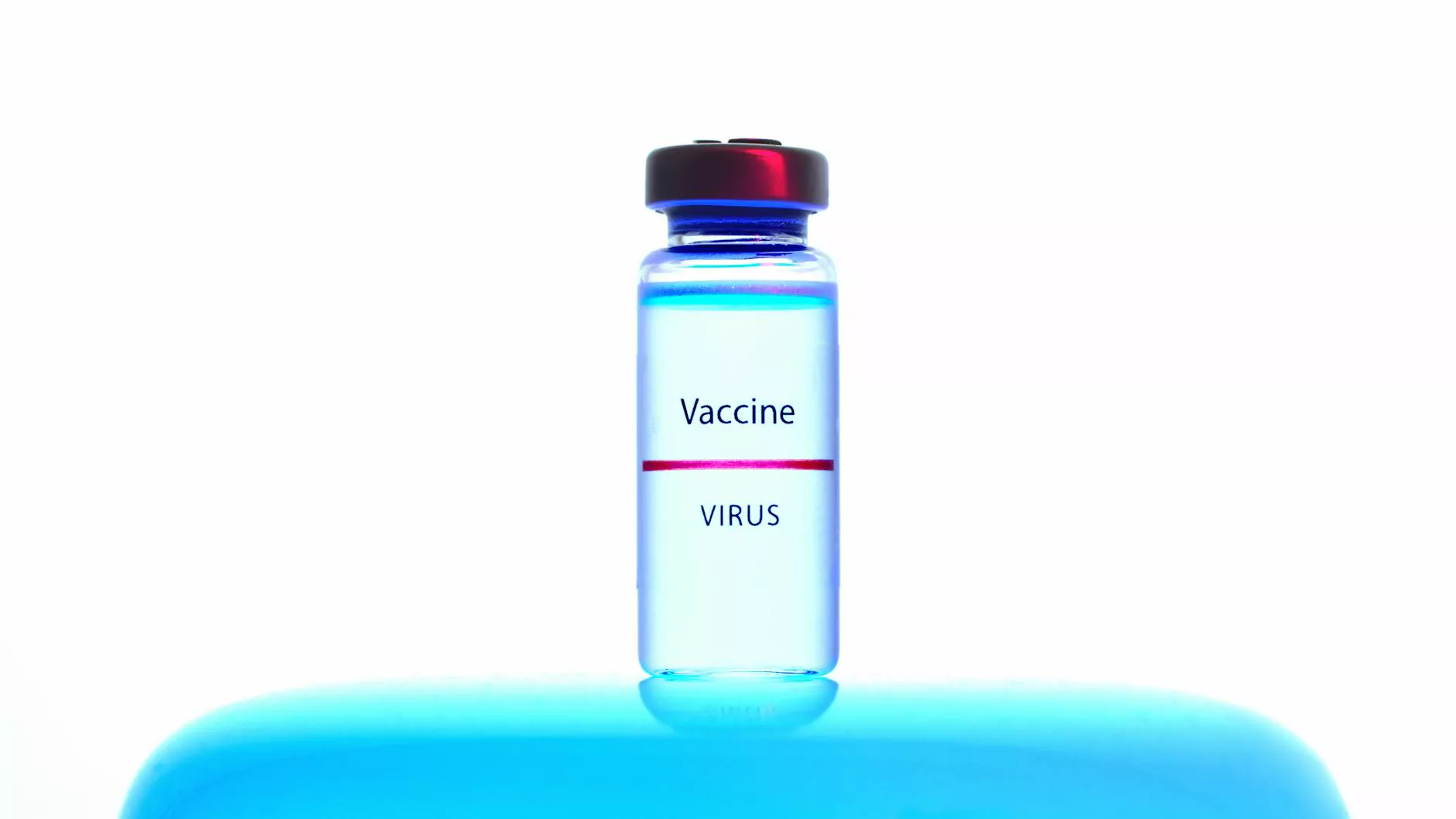
Plastic molding injection has revolutionized industries by facilitating the efficient production of various components that are integral to many products. With applications spanning numerous sectors, understanding the nuances of this manufacturing process is essential for businesses aiming to enhance their operational efficiency and product quality.
What is Plastic Molding Injection?
Plastic molding injection is a manufacturing process used to produce parts by injecting molten plastic into a mold. This process allows for high-precision, high-volume production of intricate designs with minimal waste. The basic steps involved include:
- Material Preparation: Raw plastic pellets are fed into a heated barrel.
- Melt Extrusion: The plastic is melted into a viscous state.
- Injection: The molten plastic is injected into a mold cavity under high pressure.
- Cooling: The plastic cools and solidifies into the desired shape.
- Ejection: The molded part is ejected from the mold once cooled.
The Importance of Plastic Molding Injection in the Business Landscape
For businesses, particularly in industries such as metal fabrication, adopting plastic molding injection can lead to significant advantages:
1. Cost-Effectiveness
The plastic molding injection process is highly efficient and allows for mass production, which reduces the cost per unit significantly. This is especially important for businesses that require large quantities of parts without compromising on quality.
2. Enhanced Precision and Quality
Modern injection molding machines offer high precision, enabling manufacturers to produce components that adhere to strict specifications. This quality assurance is crucial for businesses as it minimizes defects and enhances product performance.
3. Versatile Material Options
Plastic molding injection can utilize various thermoplastic materials, tailored for specific applications. The ability to choose materials based on strength, flexibility, and other properties allows businesses to innovate and meet customer demands effectively.
Applications of Plastic Molding Injection Across Industries
The versatility of plastic molding injection lends itself to numerous applications across different industries:
1. Automotive Industry
In the automotive sector, manufacturers rely on plastic molding to create components such as dashboards, bumpers, and interior fittings that are lightweight and durable.
2. Consumer Products
From toys to household appliances, countless everyday objects are produced using plastic molding injection, allowing for vibrant designs and economic production.
3. Electronics
Products ranging from smartphones to computers often utilize injection-molded parts to enclose circuitry and support structural integrity, ensuring both functionality and aesthetics.
4. Medical Devices
The medical community benefits significantly from this technology. Plastic molded components are used in various devices, from surgical instruments to prosthetics, providing precision and sterility.
Choosing the Right Partner for Plastic Molding Injection
Selecting the right manufacturing partner for plastic molding injection is crucial for success. Here are some key considerations:
1. Expertise and Experience
Investigate potential partners for their industry experience and expertise in plastic molding processes. Companies like Deep Mould bring years of experience and a track record of high-quality results.
2. Machinery and Technology
Ensure that your partner utilizes the latest technology and equipment for injection molding. Advanced machinery will aid in achieving the best quality and efficiency in production.
3. Quality Assurance Processes
Look for manufacturers that employ robust quality control measures throughout the production process, ensuring that the final products meet all specifications and standards.
4. Customization Capabilities
Every business has unique needs. A capable manufacturer should offer customization options in terms of design and material selection to cater to specific requirements.
Future Trends in Plastic Molding Injection
The plastic molding injection industry is continuously evolving. Understanding future trends can help businesses stay ahead:
1. Sustainability
As environmental concerns grow, the industry is shifting towards more sustainable practices, including the use of recycled materials and energy-efficient machines. Companies focusing on these areas are more likely to attract environmentally-conscious customers.
2. Automation and Industry 4.0
Incorporating automation within the plastic molding injection process improves efficiency and reduces labor costs. With Industry 4.0, smart manufacturing technologies will lead to greater connectivity and data-driven decision making.
3. Multi-material Molding
Advancements in multi-material molding allow manufacturers to mix different materials in a single part, opening avenues for improved functionality and design flexibility.
Conclusion: The Future is Bright with Plastic Molding Injection
With its numerous advantages and applications, plastic molding injection stands as a cornerstone in modern manufacturing paradigms. For businesses such as those in the metal fabricators category, understanding and leveraging this technological marvel can significantly outpace competition and foster innovation.
In a world where efficiency and quality are paramount, integrating plastic molding injection into your manufacturing strategy could lead to transformative benefits. With a focus on partnering with experienced manufacturers like Deep Mould, your business can harness the full potential of this manufacturing process.
As we continue to innovate and evolve, the journey into the realm of plastic molding injection promises a bright future for businesses ready to embrace this incredible technology.