The Comprehensive Guide to Volumetric Concrete Plants
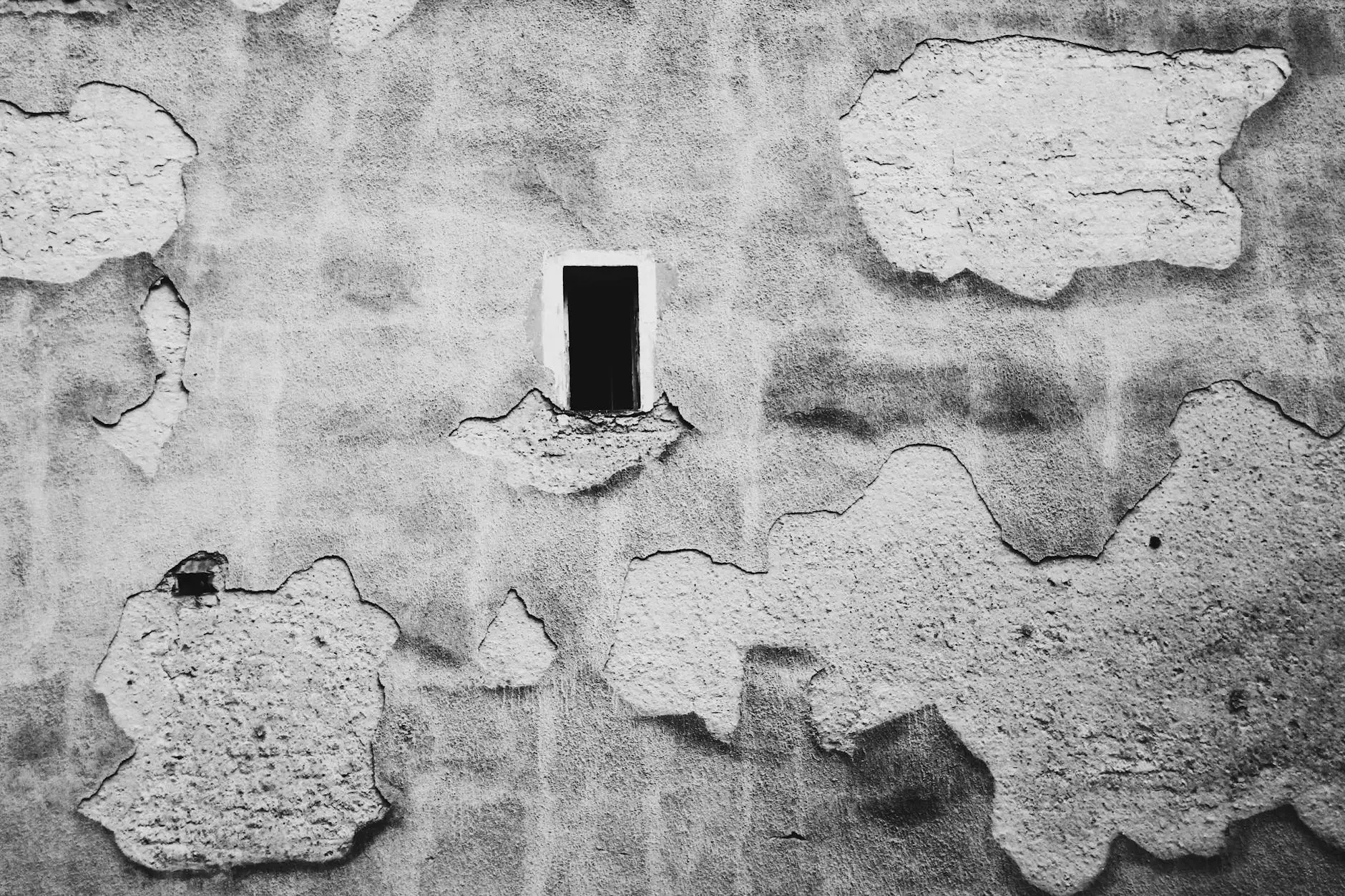
Understanding Volumetric Concrete Plants
A volumetric concrete plant represents a remarkable advancement in the field of concrete mixing and delivery. In contrast to traditional batch plants, which produce concrete at fixed intervals in a centralized location, volumetric concrete plants are designed for on-site mixing. This innovation allows for greater flexibility, efficiency, and cost-effectiveness in construction sites.
What is a Volumetric Concrete Plant?
At its core, a volumetric concrete plant consists of a mobile unit equipped with storage compartments for materials like cement, aggregates, water, and additives. The unique feature of these plants is their capability to accurately measure, mix, and deliver concrete on demand.
The Structure of a Volumetric Concrete Plant
- Cement Silos: Enclosed storage for cement.
- Aggregate Storage: Bins for sand and gravel.
- Water Tanks: Reservoirs for mixing water.
- Additive Bins: Compartments for chemical admixtures.
- Control Panel: The brain of the operation, managing mix ratios and output.
Benefits of Using Volumetric Concrete Plants
Utilizing a volumetric concrete plant can offer numerous advantages, which can significantly enhance project management and execution.
1. Flexibility
The flexibility provided by a volumetric concrete plant allows contractors to produce concrete in varying quantities and mix designs based on immediate project requirements. This adaptability minimizes waste and optimizes resource utilization.
2. Quality Control
Mixing concrete on-site enables real-time adjustments, ensuring a consistent and high-quality product. This control over the mixing process allows operators to address issues as they arise, maintaining the integrity of the concrete delivered to the site.
3. Reduced Transportation Costs
Since volumetric concrete plants are mobile, they can travel to various job sites, reducing the need for costly transportation of pre-mixed concrete. This can significantly decrease overhead expenses and logistics complications.
4. Time Efficiency
With a volumetric concrete plant, construction teams can mix and pour concrete according to schedules that suit the project needs, reducing downtime and enhancing overall operational efficiency.
5. Improved Environmental Impact
These plants can contribute to sustainability efforts by minimizing waste through precise material measurements and reducing the carbon footprint associated with transporting concrete over long distances.
Key Considerations for Selecting a Volumetric Concrete Plant
When looking to incorporate a volumetric concrete plant into your operations, consider the following factors:
- Capacity: Determine the volume of concrete required to meet your project demands.
- Materials Storage: Ensure the plant has adequate storage for all necessary components.
- Mobility: Evaluate whether the plant needs to be easily transportable between sites.
- Automation: Look for advanced controls that can enhance accuracy and ease of use.
- Maintenance Requirements: Choose a model that provides ease of maintenance and support services.
How Volumetric Concrete Plants Work
The operation of a volumetric concrete plant is relatively straightforward and can be broken down into the following steps:
1. Material Loading
Aggregate, cement, and water are loaded into the respective compartments of the plant. This can be done using grabbers or conveyor belts depending on the plant setup.
2. Measurement and Mixing
When a concrete order is placed, the operator inputs the necessary mix design into the system. The control panel then measures each component accurately based on volumetric proportions before mixing them in the drum.
3. Delivery
Once mixed, the fresh concrete is ready to be poured. The mobile nature of the plant allows the operator to drive it to the exact point of delivery on the construction site.
Applications of Volumetric Concrete Plants
Volumetric concrete plants are versatile and can be employed in a variety of construction projects, including:
- Residential Construction
- Commercial Builds
- Road and Highway Projects
- Bridge Construction
- Infrastructure and Utilities
- Civic and Community Services
Challenges and Solutions in Volumetric Concrete Plants
While volumetric concrete plants offer numerous benefits, there are also challenges to consider:
1. Operator Training
Effective operation of a volumetric concrete plant requires skilled personnel. Investing in training programs can ensure teams are well-prepared to handle the equipment and maximize its potential.
2. Regulatory Requirements
Operators must be aware of local regulations regarding concrete mixing and environmental standards. Staying compliant is essential to avoid penalties and ensure public safety.
3. Equipment Maintenance
Regular maintenance schedules should be established to prevent breakdowns. Investing in high-quality equipment and establishing a maintenance routine can mitigate downtime.
The Future of Volumetric Concrete Plants
As technology advances, the volumetric concrete plant landscape continues to evolve. Innovations such as:
- Smart Technology: Integration of IoT devices for real-time monitoring and diagnostics.
- Automated Mixing: Enhanced automation for reducing human errors and increasing production rates.
- Eco-friendly Solutions: Development of greener concrete mixtures and sustainable practices.
These advancements promise to further improve the efficiency, cost-effectiveness, and environmental impact of volumetric concrete plants in the construction industry.
Conclusion
In summary, a volumetric concrete plant stands as a vital asset in modern construction methodologies. From flexibility and quality control to reduced transportation costs, these plants offer unparalleled advantages. As we look to the future, embracing innovations and understanding the challenges associated with their use will ensure that businesses remain competitive in an evolving market.
For further information or to explore how you can implement a volumetric concrete plant into your operations, visit polygonmach.com and stay ahead in the construction industry.